Starting a screen printing business requires careful planning and the right set of tools. The essential tools for screen printing help ensure that your business operates efficiently, delivering high-quality prints to customers. With the right equipment, you can tackle various printing jobs, from custom t-shirts to signage. This post will cover the basic tools you need to begin a successful screen printing business.
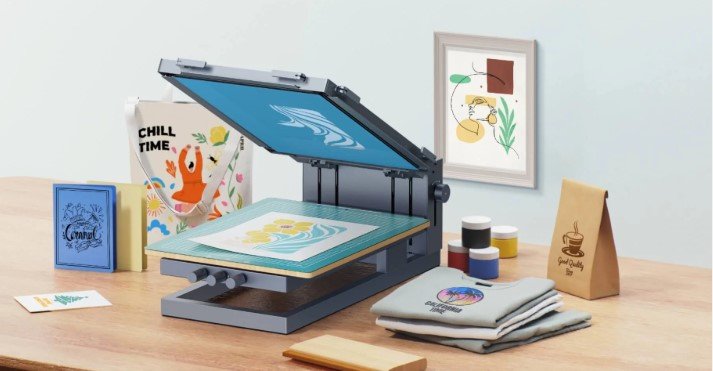
Screen Printing Press
The screen printing press is the core of any screen printing operation. It is the tool that holds the screen and ensures precise alignment when applying ink. There are several types of presses, including manual, automatic, and semi-automatic presses. For beginners, a manual press can be a great choice as it offers control over the printing process at a lower cost. However, as your business grows, you may want to invest in an automatic press to speed up production. Regardless of the type, a reliable screen printing press is essential for accurate and consistent prints.
Screens and Frames
The next essential tool is the screen and frame. Screens are made of mesh fabric stretched tightly over a frame. They hold the stencil or design through which the ink passes. You will need a variety of screen sizes to accommodate different designs and printing areas. The mesh count of the screen plays a crucial role in the final print quality. Higher mesh counts are suitable for detailed designs, while lower mesh counts are better for larger prints. A strong, durable frame ensures the screen stays in place during printing.
Inks and Chemicals
Inks and chemicals are vital components in screen printing. The right type of ink ensures that your prints are vibrant, durable, and suitable for different fabrics or surfaces. For fabric printing, plastisol ink is a common choice, known for its opacity and durability. Water-based inks are another option, offering a softer feel but requiring more careful handling. In addition to inks, you will need chemicals such as emulsion for coating screens, screen cleaners, and degreasers to prepare your screens. Make sure to choose inks and chemicals that align with the materials you plan to print on and the specific effects you want to achieve.
Exposure Unit
An exposure unit is used to burn the design onto the screen. This tool plays a key role in transferring your artwork onto the screen mesh. The exposure unit uses UV light to expose the emulsion-coated screen to the design. The areas of the screen covered by the design remain unexposed, while the other areas harden, creating a stencil. A high-quality exposure unit ensures that your designs are crisp and accurate. Investing in a good exposure unit will save time and effort in your production process, improving the overall quality of your prints.
Curing Equipment
Curing equipment is essential to ensure that the ink dries properly and adheres to the fabric or material. A conveyor dryer or flash dryer is typically used to cure the printed design. The dryer applies heat to the ink, making it durable and resistant to wear. A conveyor dryer moves garments or other materials through the heat chamber, while a flash dryer focuses heat on specific areas, ideal for quick curing between printing layers. Proper curing is crucial to ensure the longevity of your prints, especially for fabrics that undergo regular washing.
Conclusion
Starting a screen printing business requires investing in essential tools that ensure your production process is smooth and efficient. From a reliable screen printing press to curing equipment, each tool plays a crucial role in creating high-quality prints. As your business grows, you may need to expand your equipment to meet increasing demand. However, starting with these basic tools will give you a solid foundation for success in the screen printing industry.