Screen printing is a versatile and popular technique used to create vibrant designs on various materials. However, like any printing process, it comes with its own set of challenges. These challenges can affect the quality of prints, production efficiency, and overall workflow. Understanding these common issues and learning how to solve them is essential for ensuring smooth operations and high-quality results. In this post, we will explore some of the most common challenges in screen printing and provide effective solutions for each.
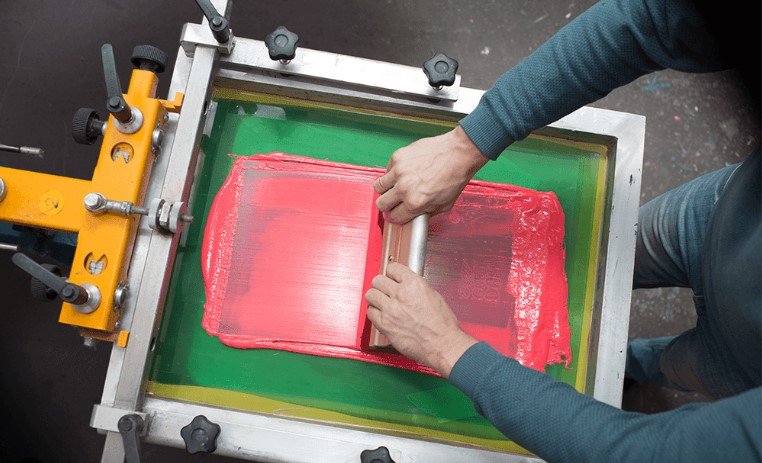
Ink Smudging and Bleeding
One of the most common problems in screen printing is ink smudging or bleeding. This happens when the ink spreads beyond the intended design, resulting in blurry or inconsistent prints. Ink smudging can be caused by several factors, including using the wrong ink type, overloading the screen with ink, or improper curing.
Solution: To prevent ink smudging, start by choosing the correct type of ink for your material. For example, use plastisol ink for textiles and water-based ink for fabrics that require a softer feel. Ensure that you do not overload the screen with ink, as excess ink can cause it to bleed. Finally, make sure the print is properly cured, as insufficient curing can cause the ink to smudge. Invest in reliable curing equipment and test the curing process regularly to ensure optimal results.
Inconsistent Print Quality
Inconsistent print quality can be a frustrating issue for screen printers. This problem can manifest as uneven color distribution, irregular edges, or blurry lines. It may occur due to a variety of reasons, such as improper screen tension, uneven pressure during printing, or a worn-out screen.
Solution: To achieve consistent print quality, start by checking the mesh tension. Make sure that the mesh is evenly stretched across the frame, as inconsistent tension can cause uneven prints. Also, pay attention to the pressure you apply when pulling the squeegee. Too much or too little pressure can cause the ink to flow unevenly. Regularly inspect and replace worn-out screens to ensure optimal performance. Lastly, test the print on sample material before beginning large-scale production to identify any potential issues early.
Screen Clogging and Blockages
Screen clogging is another common challenge in screen printing. It occurs when ink gets trapped in the mesh, preventing it from passing through during the printing process. This can happen when the mesh is too fine, or when the ink is too thick or improperly mixed. Clogging can lead to poor-quality prints and waste of materials.
Solution: To prevent screen clogging, make sure to choose the right mesh size based on the design and the type of ink used. Finer mesh screens are ideal for detailed designs, while coarser mesh works better for larger, bolder prints. Keep the ink at the correct viscosity by mixing it thoroughly before use. If you experience clogging, clean the screen immediately using a suitable cleaning solution or a pressure washer to remove any trapped ink.
Conclusion
Screen printing is a powerful technique, but it does come with its set of challenges. By understanding these common issues—such as ink smudging, inconsistent print quality, screen clogging, uneven ink coverage, and color mismatch—you can take proactive steps to avoid them. The key to overcoming these challenges lies in using the right materials, maintaining equipment properly, and carefully monitoring each step of the printing process. With the right solutions in place, you can achieve high-quality, consistent prints and improve the efficiency of your screen printing operations.